Trimtab3X3 Human Powered Vehicle
The following are excerpts from my Master's thesis, which focused on the subject of Slow Design and culminated in the design and prototyping of a human/electric hybrid vehicle. Click here to download the complete document.
SOLUTION
Trimtab is a 3X3 human/electric hybrid vehicle designed for intracity travel on conventional roadways. It is designed for intracity commuters whose commute is too long or whose fitness level is too low for a conventional bicycle. Like its namesake, the Trimtab is intended to steer these users toward a healthy and sustainable commute.
The vehicle is designed with a lightweight, tubular frame made from aircraft grad aluminum. It uses modular fabric skins to provide different levels of protection, seasonally — insulated for winter, breathable for summer, waterproof all-year-round. Trimtab is lean-steered with control handles to provide an exhilarating driving experience.
OPPORTUNITY
Conventional automobiles contribute to traffic congestion, urban sprawl, community isolation, global warming, obesity and respiratory diseases, traffic deaths, and many other problems.
The answer to efficient, healthy low cost, and zero pollution transportation over intracity distances is simple — the bicycle. But most of us aren't fit enough to bike to work everyday or confident enough to ride in fast-moving suburban traffic, nor do we enjoy riding in bad weather.
There is an opportunity for an intracity commuter vehicle that combines human and auxiliary power in am efficient and versatile package that takes the edge off of bicycle commuting.
“Something hit me very hard once, thinking about what one little man could do. Think of the Queen Mary — the whole ship goes by and then comes the rudder. And there’s a tiny thing at the edge of the rudder called a trimtab.”
Concept Sketches & Preliminary Design
Trimtab’s design began along a more conventional velomobile trajectory but shifted to a more radical design when I realized that the result would be financially inaccessible to most users. What started as a conventional tadpole trike with a strip-planked composite monocoque fairing eventually shifted to a simpler, more accessible design incorporating a welded aluminum frame with stretched fabric skins. The sketches below show some of the preliminary design exploration with which the project began.
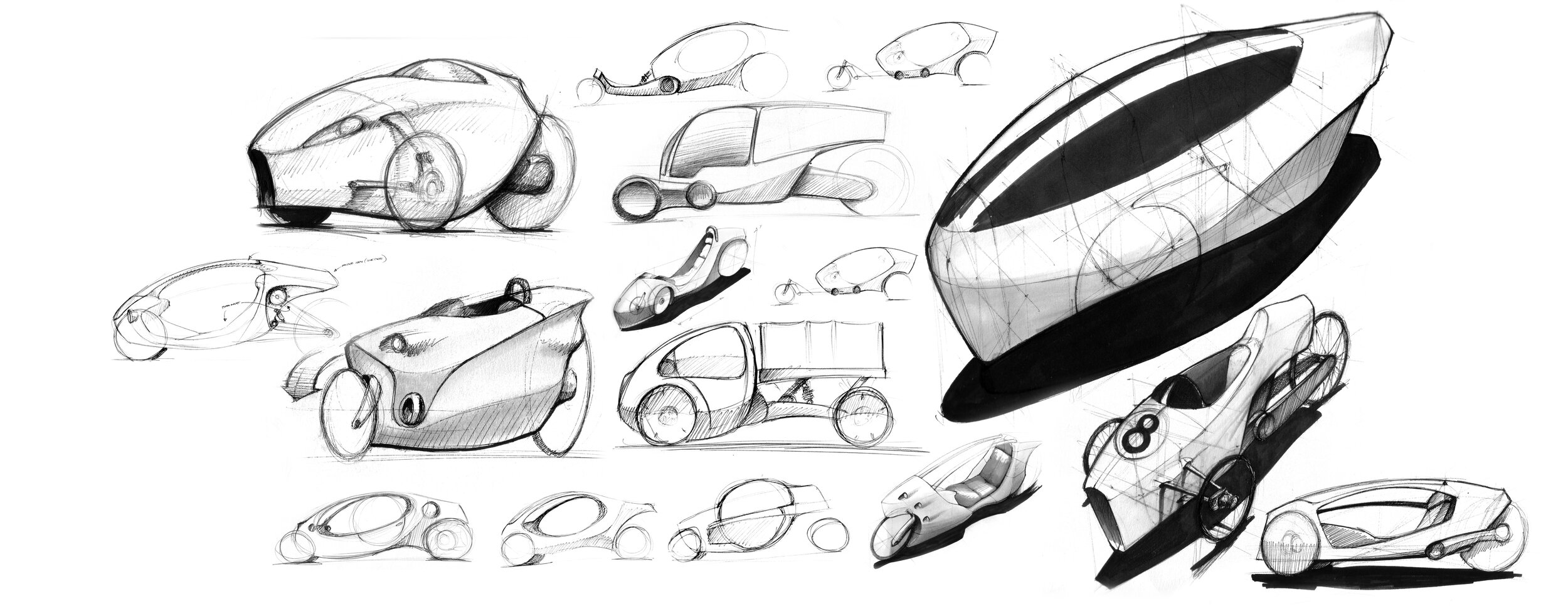
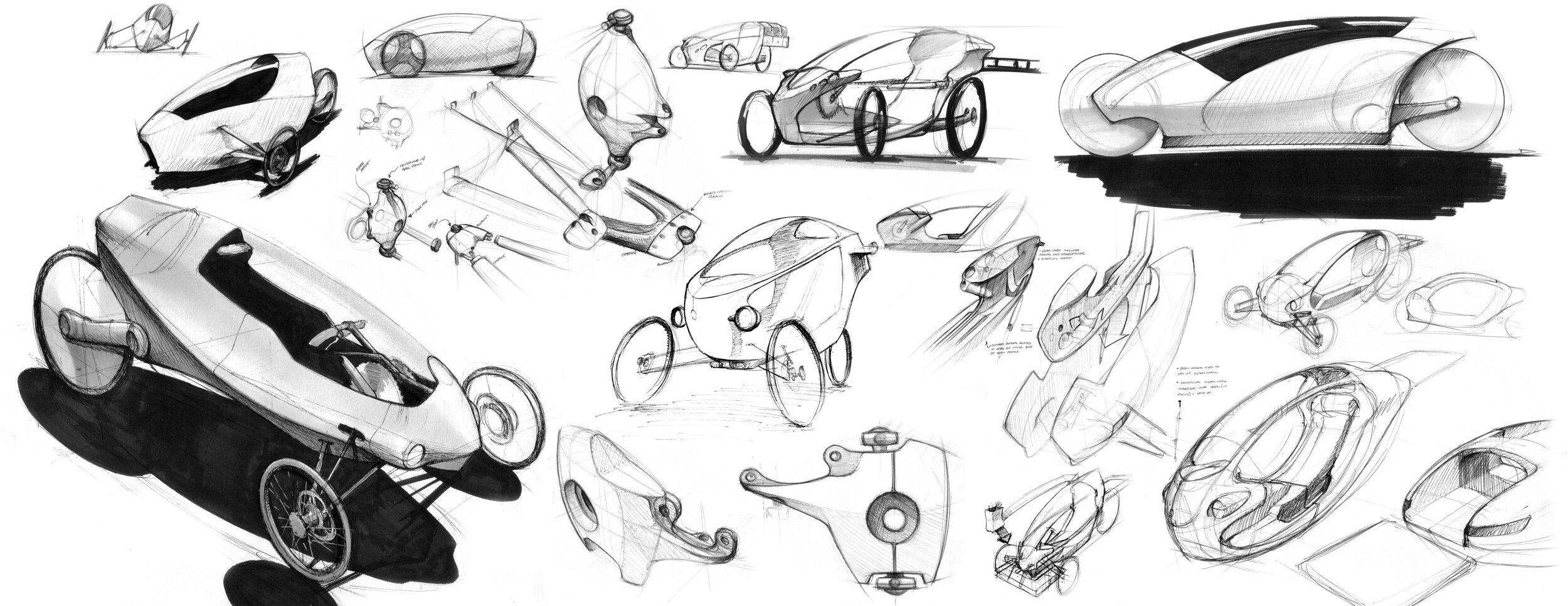


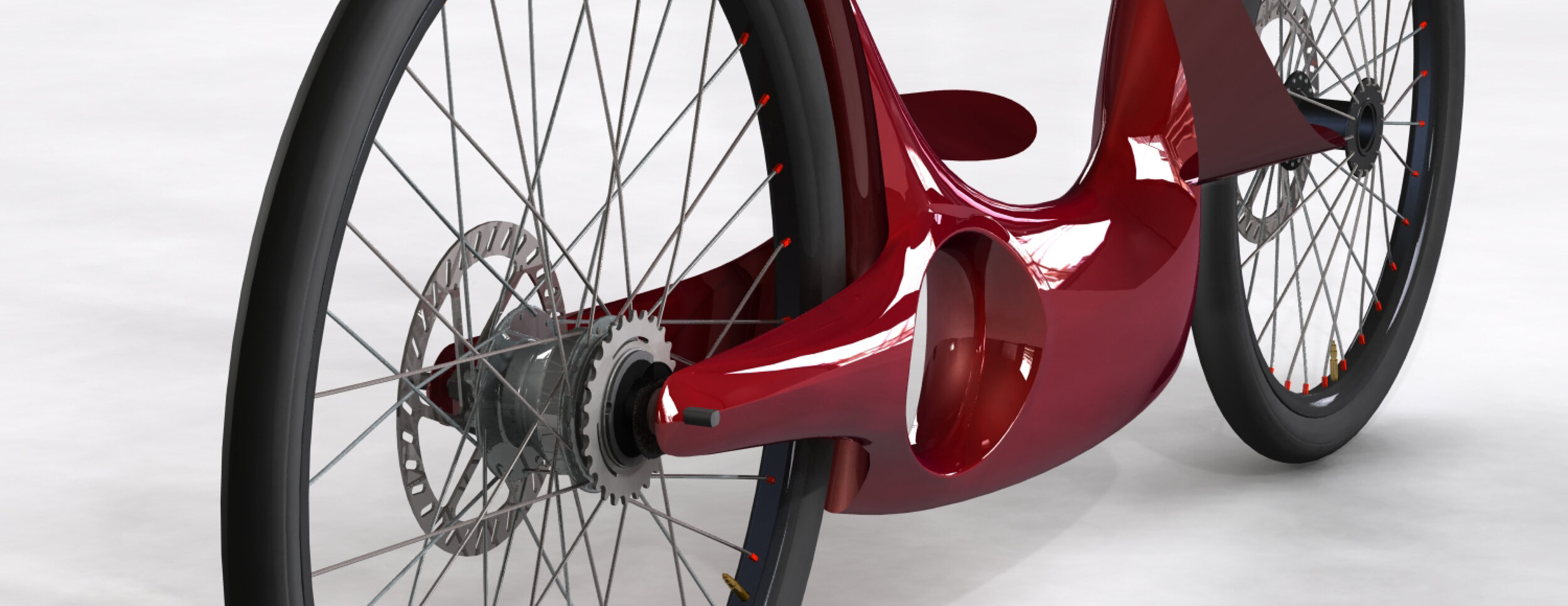
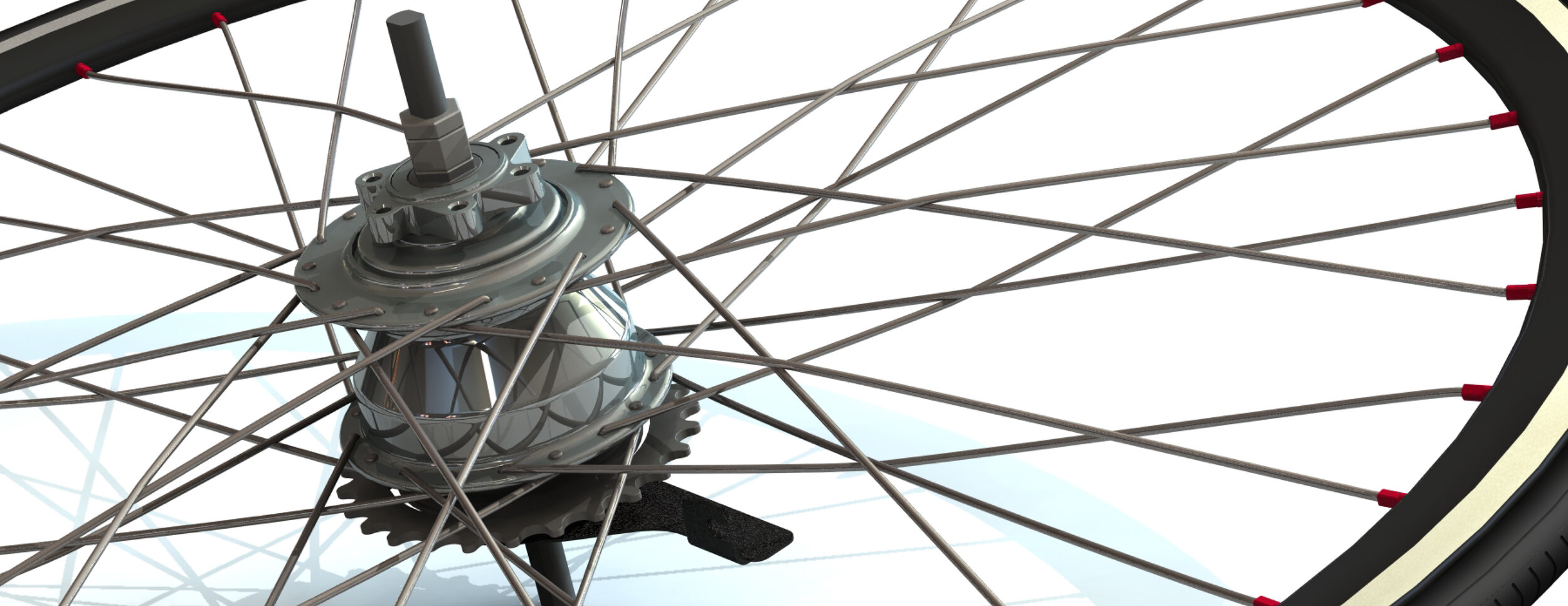
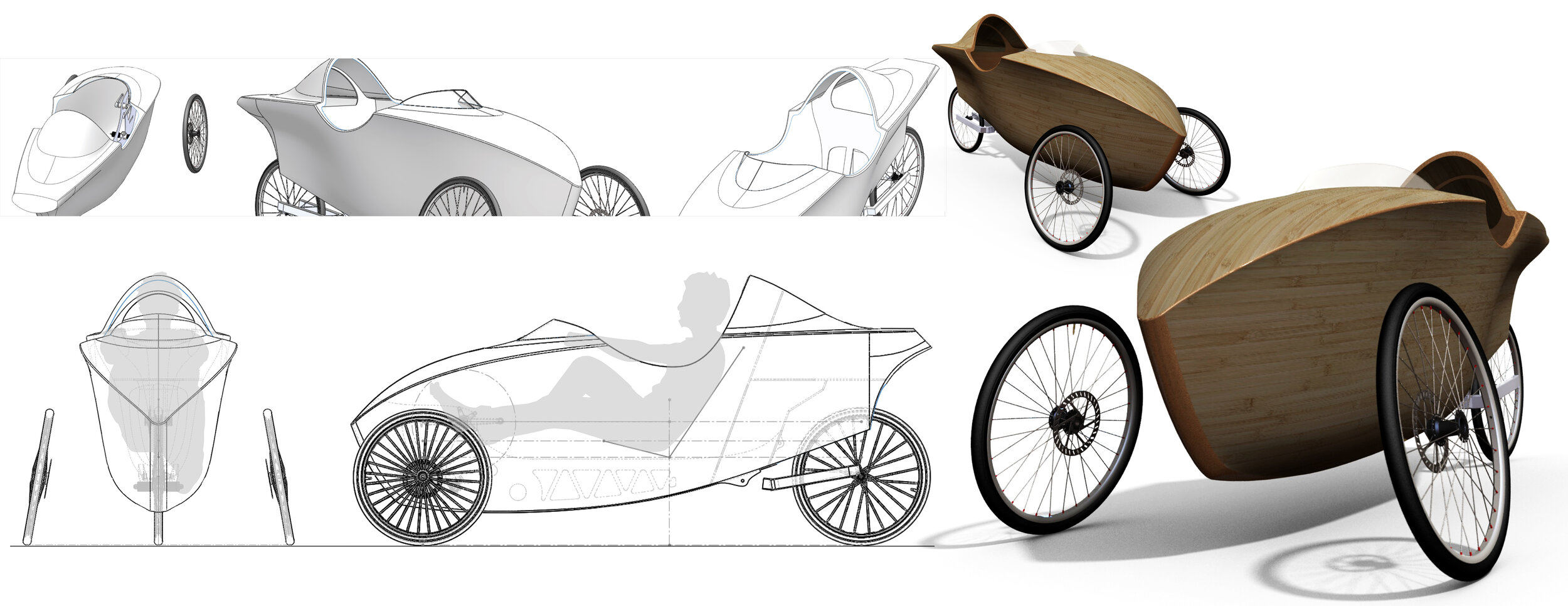
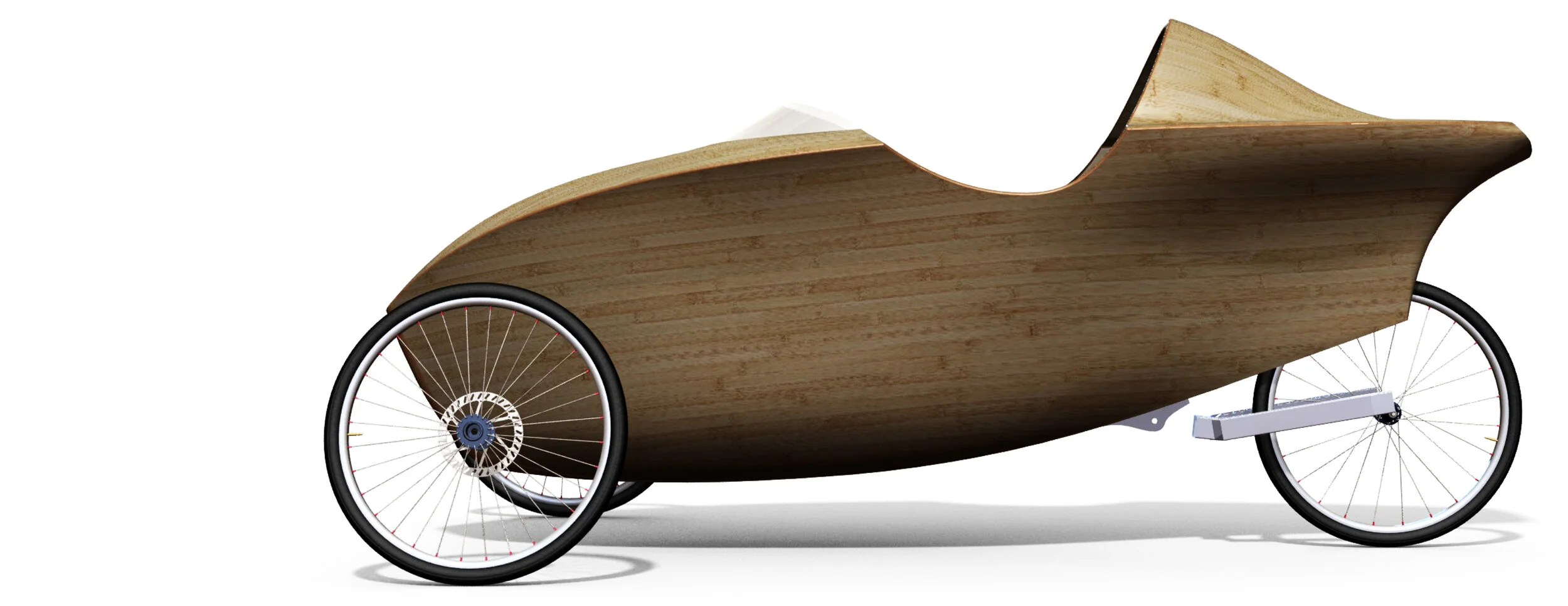
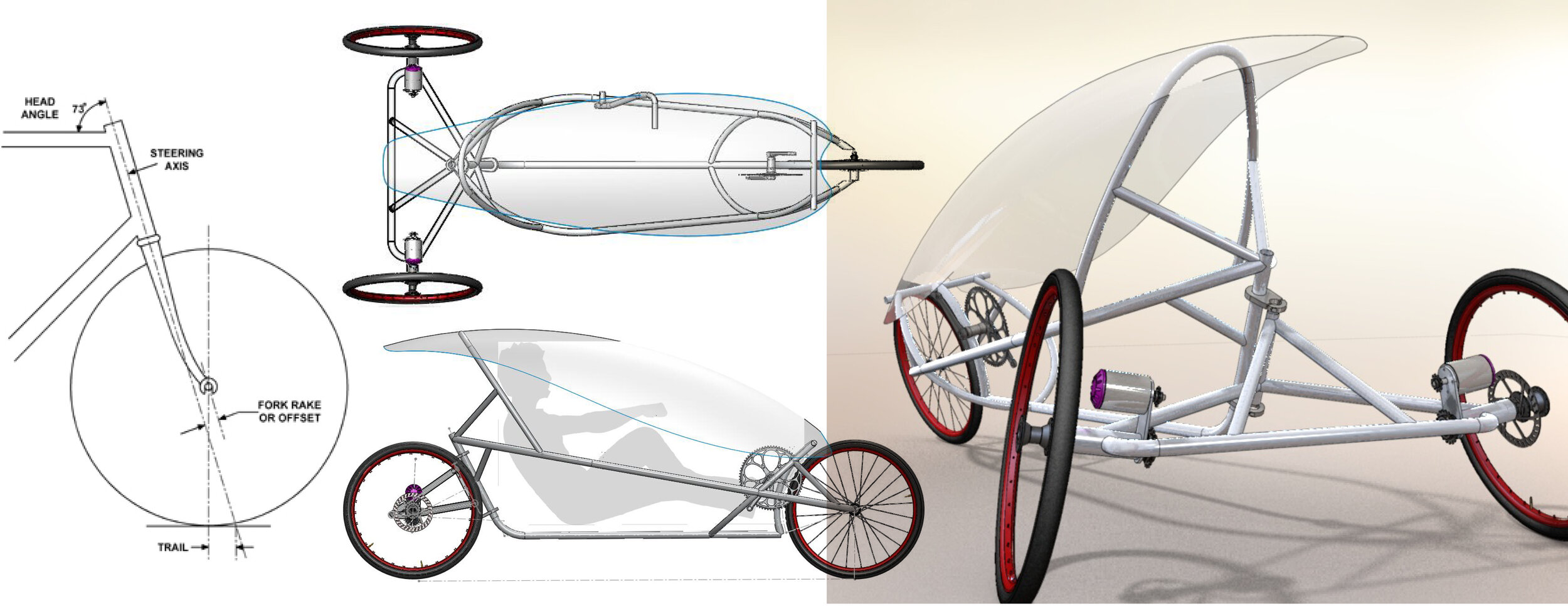
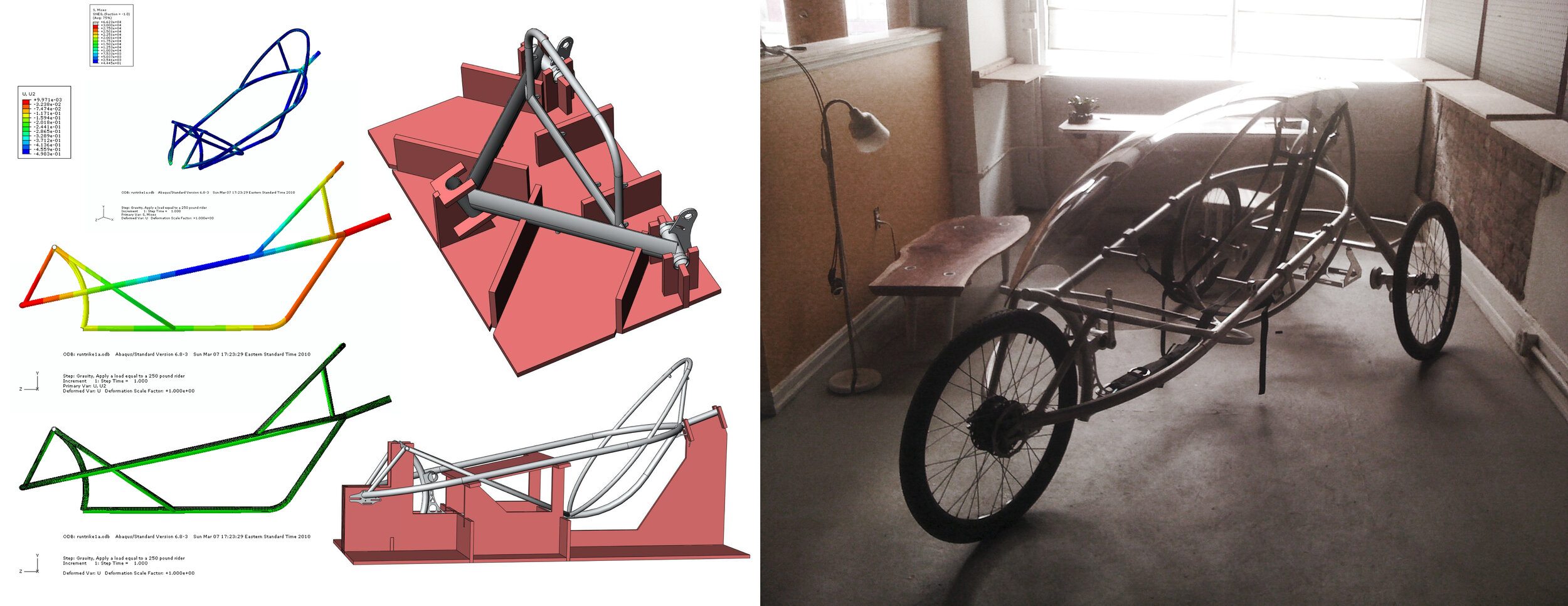
The photos below are excerpted from the build of the first version of this vehicle. This design was based on the “slow design” philosophy. It was to be constructed of strip-planked wood machined from FSC-certified timber. The composite fairing was to be encased in a layer of silk impregnated with a UV-curable bio-resin. (A tanning bed was purchased to cure Ecocomp resin from Sustainable Composites LTD.) The design was to incorporate a conventional tadpole velomobile format with streamlined fairing, dual wishbone front suspension and electric assist. \
As the fairing neared completion, I determined to abandon this design and return to the drawing board. Even as I began construction on this design, I was reading about the history of the Arts & Crafts Movement — a philosophical and design movement with many parallels to “slow design.” I realized that, like many of the products of the arts & crafts movement, the outputs of this project would be financially inaccessible to the vast majority of users. I resolved to start the design over from scratch using other hand-crafted process — welding and sewing — that could be performed
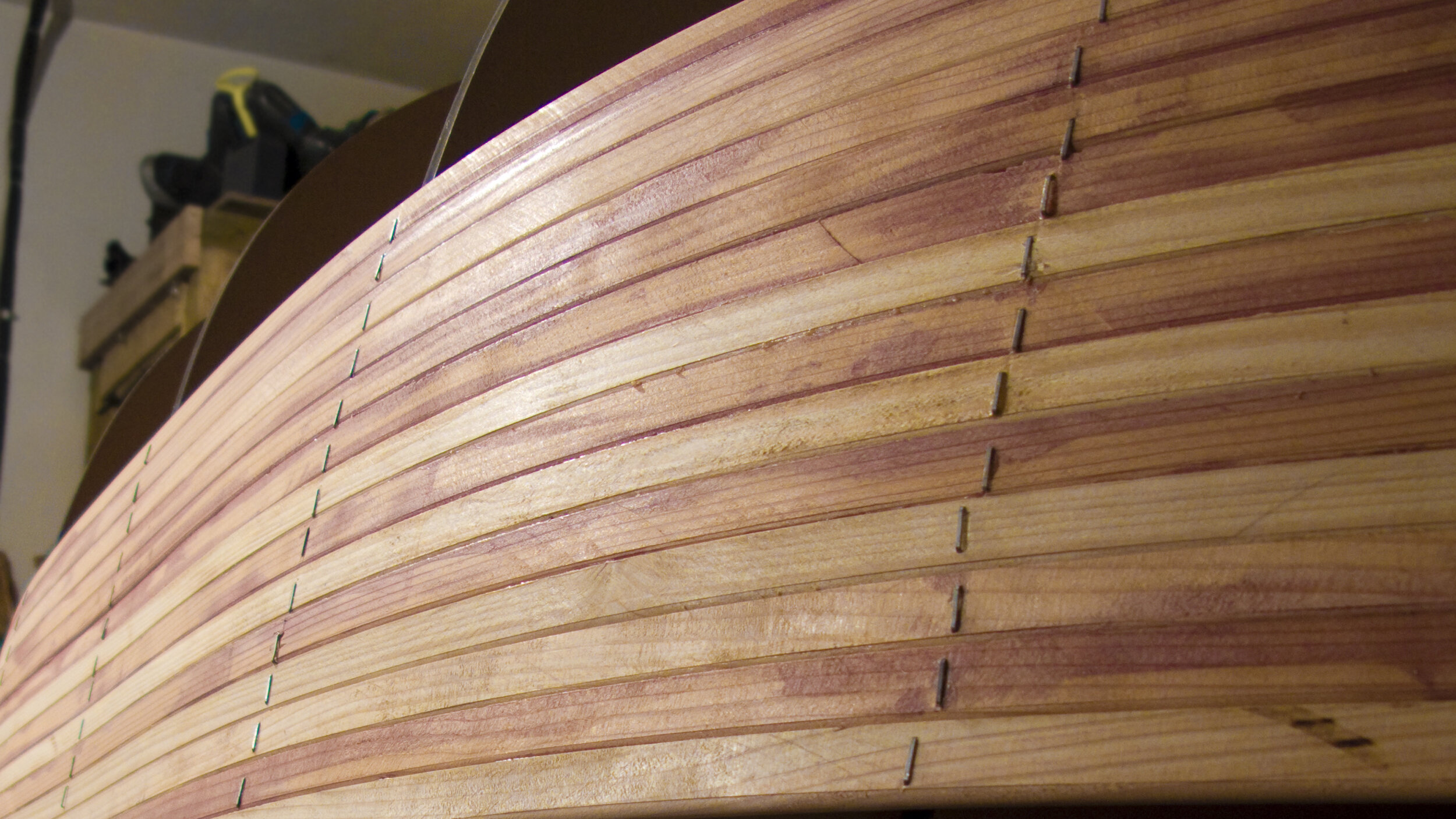
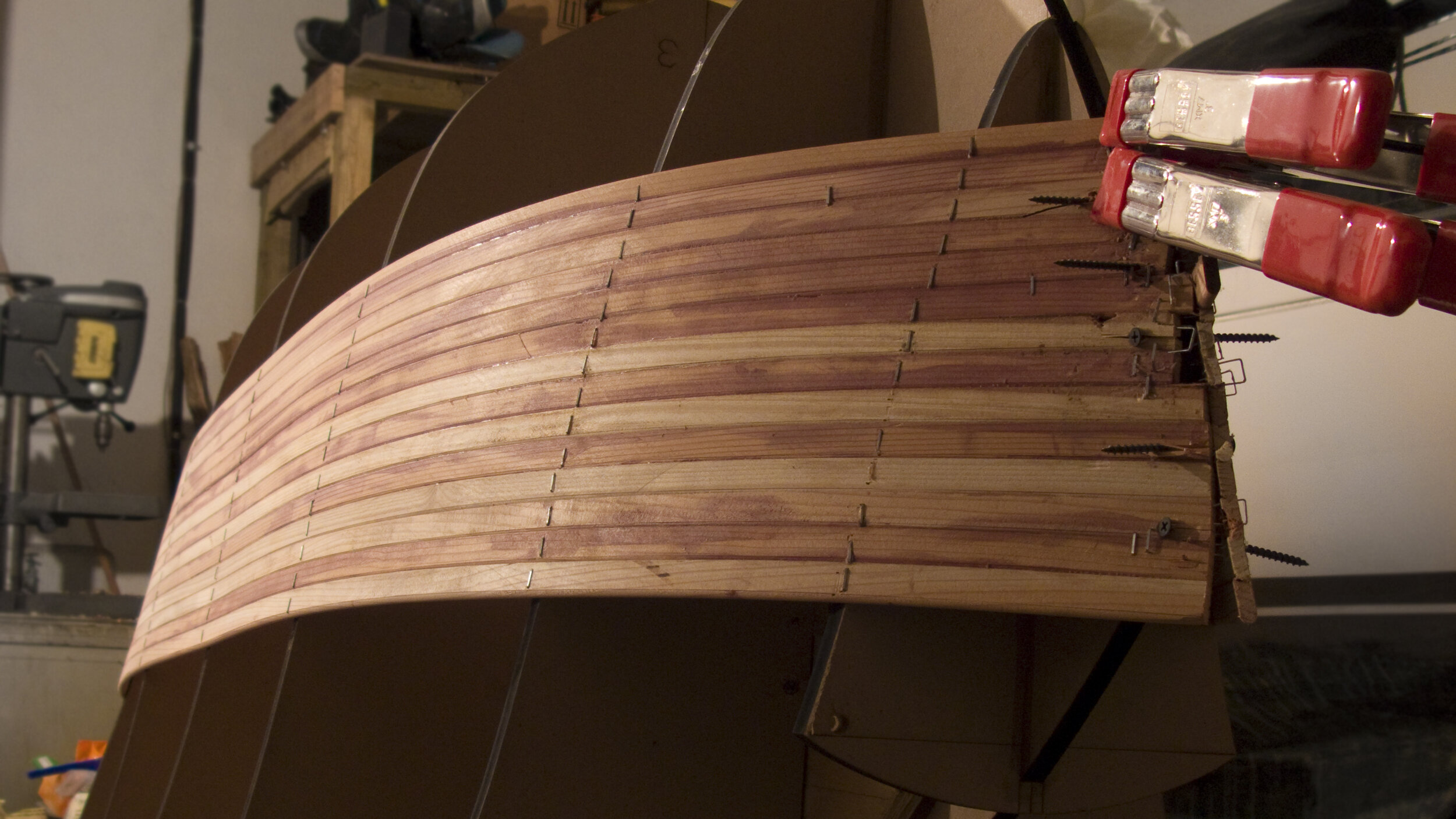

Proof-of-Concept Prototype
This project culminated in proof-of-concept (POC) prototype that proved the effectiveness of this unique lean-steering frame geometry as a low impact automobile alternative. The series of photos below were taken at various stages during the build of this vehicle. Special thanks are due to Haskell Simpkins (who brought his expert welding skills to the project), Mark and Rachel Bennett (a father/daughter duo who brought engineering expertise), Clint Haynes (who offered his lab and equipment to facilitate the project), Patrick Harrell (who performed a basic stress analysis on the frame’s design), and Matt Boehle (whose lent his amazing machining knowledge and equipment to create the unique hubs around which this design revolved).
Once complete, the vehicle was in the hallways of DAAP and on the road. Even with heavy, sealed lead acid batteries and a primitive gear train, the POC performed admirably. With its lowest gearing, it enabled its rider to climb the steepest hills in Cincinnati at a pace that made it safe enough to operate in traffic. Its unique lean-steering performed well on city roadways, and it was a blast to drive! The images below were taken at the Northside 4th of July parade in 2011 and at a trade show in which the vehicle was showcased that same year. The videos were shot during the build process to document progress as the prototype was developed.
NETWORK DIAGRAMMING TO IDENTIFY WEIGHT SAVINGS
The images here are from a short effort to identify areas of potential weight savings for the finished prototype. During this process, a Gephi network diagram was created to document the connections (between parts) that would require design changes if one or the other part was modified. Every part was then analyzed for weight, and the nodes of the diagram were sized to reflect that weight. This process roughly illustrated the cost — in terms of design changes — that would be required to save weight in each part. This process identified parts with the greatest potential for weight reduction that would require the fewest changes to the vehicle.
CAD Download
One thing I often see inventors struggle with is the subject of intellectual property (IP). There is such an obsession with IP in this country, inventors are often more concerned with attaining a patent than they are with developing a product that meets an unmet need, can be manufactured and sold profitably, or for which there is an actual market. Everyone has a product idea, but very few people actual reduce their idea to practice. And while I understand the need for IP, I also feel that certain technologies — particularly those for which there is no real market — are better shared than cloistered.
This project was completed for the purpose of a Masters Thesis. It is my hope that its design will help inform others who want to experiment with similar geometry for their own purposes. For those who are interested in creating vehicles of similar design, I’ve made the 3D CAD of this design available for download. (Files are in STP and EASM formats.) These models are released into the public domain and are free to anyone for any purpose.
Note: This design was developed as a proof-of-concept prototype to test the geometry and format of this unique design. Elements of this design have not been tested to the level necessary to produce a sufficiently safe vehicle for use on public roadways. If you elect to build a vehicle based on any aspect of this design, you do so at your own risk.
To download these drawings, please fill out the form below. In doing so, you agree to protect, indemnify and hold Pixel & Timber harmless from and against liability, expenses and damages that result from the use of these drawings.
USE AT YOUR OWN RISK: This website is for informational purposes only. The use of any vehicle may result in damage, injury or death. Consult an engineer before using any object produced from these drawings. By voluntarily undertaking to download these drawings, you assume the risk of any resulting injury that results from their use.
NO WARRANTIES: All of the information provided on this website is provided "AS-IS" and with NO WARRANTIES. No express or implied warranties of any type, including for example implied warranties of merchantability or fitness for a particular purpose, are made with respect to the information, or any use of the information, on this site.
UPDATE!
For anyone who has downloaded the CAD above and is experimenting with this design: These push-pull cables look like nice alternatives to the (leaky) hydraulic cylinders I used on the original prototype.
https://www.mcmaster.com/3125K526/